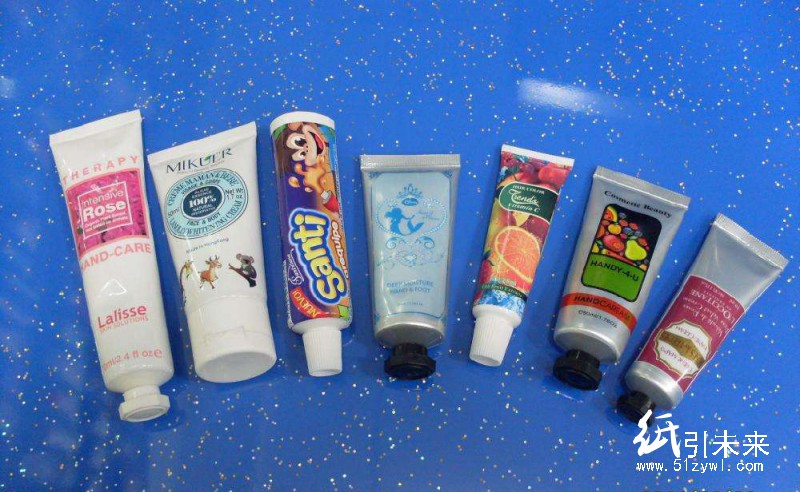
图片来源于网络
1、白度差
现象:
印刷后油墨表面呈灰或微黄色。
原因:
油墨中所用钛白粉白度不好,连接料颜色太深,影响颜色;不耐烘烤温度,泛黄,增白剂、整色剂用量不够。制造过程引入脏色。
解决办法:
油墨中加入表面纯白的钛白粉,最好使用不泛黄,稳定性好,遮盖力好的金红石钛白粉;使用色泽很浅的树脂油,或用这样的树脂油调节墨性;严格掌握烘烤温度和时间,避免过分高温和长时间烘烤;调入冷色调整色剂(酞青蓝,群青)或调入暖色剂(紫红、青莲、洋红)微量,可以使涂层显得更白;严格清洁,防止串色或混入其它色,压力不要太大,否则会引起摩擦变灰黑。
2、粉化
现象:
滚涂后的墨膜,轻轻一擦即掉色粉,暗淡无光。
原因:
由于树脂不能很好的包裹颜料的树脂;颜料量大,树脂量大,树脂不能很好的包裹颜料形成光亮的墨膜。
解决办法:
增加树脂量,重新调配油墨;已经滚涂并及早发现的时候,可以滚涂一次亮光油来弥补。
3、桔皮
现象:
涂层表面形成桔子皮一样的纹路。
原因:
由于溶剂馏程过宽,迅速蒸发的部分多,滚涂后,油墨尚未流平。也是由于这种原因阻碍了流平,因而形成了表面不平坦的现象。由于油墨所用树脂太少,内聚力大,流平性不好。
解决办法:
补充馏程高的溶解和改善流平性能的流平剂,如辛醇等;增加流动性能好的蓖麻油醇树脂,改善油墨平性。
4、流挂
现象:
滚涂以后,将印品置于架上,或烘干后,看到油墨流成一道一道,并有集中在某一处的形状,不平滑,亮光差。
原因:
是油墨太稀并且流平性不好;油墨太稠并流平性不好,比重太大。
解决办法:
调整油墨粘度,使其滚涂以后,在流动过程中向四周铺开。改善油墨内聚力,使之不因流平收缩成线。调整粘度到适当程度,不要太稠,或太稀。
5、露底
现象:
滚涂后,金属上墨层不厚实,能看得见铝管或显铝管拉伸痕迹,或在滚涂辊离开后留下暴露了金属管色的一条空线。
原因:
油墨粘度过小,遮盖力小,压力大,即滚涂辊和软管间距太小,油墨对金属粘附力太小。
解决办法:
将油墨粘度调整到85~95秒/25℃,不要低于60秒/25℃,适当调整滚涂压力,增加给墨量。增加对管子粘附性好的环氧或醇酸树脂。
6、折裂、脱落
现象:
滚涂墨层干燥后,在封底口和使用中折挤内装物时,墨层龟裂或成粉末状脱掉,露出金属管。
原因:
墨层干燥后,成脆硬的涂层。这主要是干燥剂加入量太多;所用树脂性质太脆;白色料含量过高。油墨过稠,墨层过厚。烘烤温度过高,时间过长均会形成不柔韧的皮膜。
解决办法:
在加入燥油时,尽量要少,使油墨层烘烤后,形成柔韧的皮膜,要经过一些试验取得适合当地的条件;针对墨中树脂脆硬之弊,应调入增塑剂邻苯二甲酸二丁酯,或配以醇酸,胺基等柔韧性好的树脂;降低白色颜料含量,以不影响遮盖力和白度为准。烘烤温度不能太高80—90℃为宜,时间不能太长,25~30分钟即可。
7、针孔
现象:
滚涂后皮膜存在着很小的透底的小孔,如用针孔的一样。
原因:
由于油墨表面张力大,对金属管湿润不好,或金属管上油污太对排斥油墨;由于溶剂配比不当,特别是蒸发快的溶剂,猛烈冲出,形成旋涡;油墨中混入大量气泡,烘烤中气泡破裂;油墨连结料中存在着溶解不完全的小颗粒与颜料带有相同电荷,互相排斥干燥。这些因素均会造成透底的小孔。
解决办法:
首先采用擦洗之法,使金属管干净;加入快干,慢干比例适当的溶剂,使蒸发速度比较缓和;加入降低表面张力的溶剂或稍降低粘度,使油墨与金属充分浸润;均匀墨,传墨辊上距离缩小,使油墨内气泡打破,打均匀后再印刷。