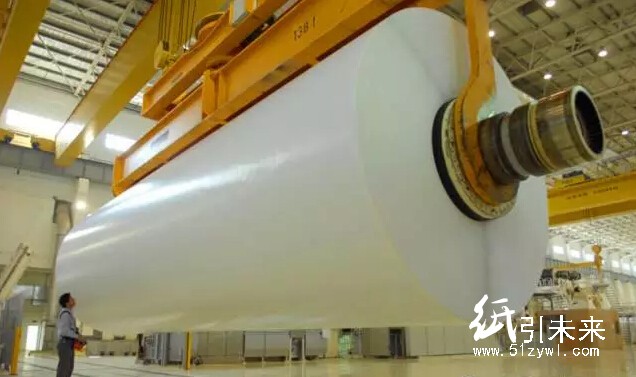
近年来,印刷技术和印刷装备不断更新发展,印刷速度越来越快,特别是彩色印刷机采用了高黏度的油墨复色印刷,就更迫切要求纸张表面强度和耐水性进一步提高。当前文化纸行业市场竞争激烈,一些企业通过提高加填量来降低产品成本,但当加填量达到一定程度时,就会加剧文化纸印刷时的掉毛掉粉。
原因分析
在印刷厂,看到掉毛掉粉的原因有的是从纸张表面带有的粉尘引起,也有的由于纸张内在强度不够引起。在印刷时,纸面上的纤维毛(纤维碎片)和填料被油墨黏下来后,纸面上应有油墨的地方,留下了白色斑点,黏下来的纤维毛、填料等堵塞印版。
降低掉毛掉粉的措施
1、加强对切纸过程的管理,减少切纸过程产生的粉尘
造成印刷过程的糊版,一部分是纸张在切纸过程中(包括复卷)产生的粉尘、纸屑掉到纸面上,在印刷时黏到胶版上引起的。
为了减少这部分的粉尘和纸屑,一方面改用了材质更好的圆刀,对已经钝了的圆刀和长刀及时更换;再者加大了切纸机上的除尘设备的抽吸力,在一些粉尘和纸屑集中的部位,加装了挡尘装置,把切纸时产生的粉尘和纸屑尽可能地抽吸完,减少粉尘、纸屑飞到纸页和地面上;
另外新建了一间数选间,把切纸间和数选间分开,避免在切纸时产生的粉尘和纸屑飞到已经数选好的产品上;同时要求操作人员每天在工作完成后对现场和设备进行彻底的清理,规定清理时现场没有产品堆放或是已经对产品加盖塑料薄膜。
2、消除产品的静电吸附
有很多的粉尘和纸屑能吸附到纸面上,而且吸附上去后就不容易掉了,有的印刷企业虽然在印刷前进行晾纸处理,但粉尘和纸屑也掉不完。分析认为是产品带有静电。
应对措施:严格控制产品的水分,不能低过质量控制指标;在纸机的干燥部位,聚脂干网改用干毯,并在纸机上的相应部位加装消除静电的装置;在气候干燥时,适当增加抄纸车间的湿度,严重时还需要在浆内加入一定量的抗静电剂。对产品调整前后不同定量的产品试印结果如表1。
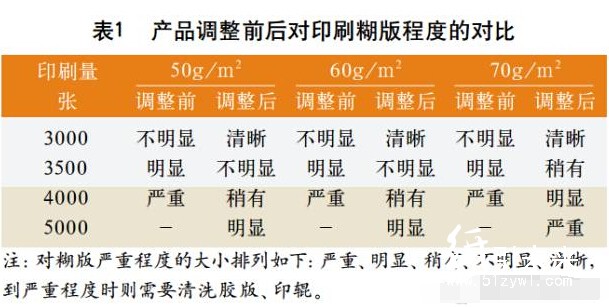
对试印结果进行分析,调整前的产品印刷到3500张时,印刷胶版就开始有些白了,但印刷出来的图文还比较清晰,当印到4000张时,胶版就很白了,对印刷出来的图文的清晰度已经有大的影响了,需要对胶版进行清洗。从表中数据可知,通过这次调整,把对印刷的影响提高了1500张左右,工作取得一定的成效。
另外,产品的定量越大,越容易糊版,分析原因:定量大的产品因灰分高容易糊版;在同一台纸机上生产的产品,相对来说,定量越大,产品的均匀度越差,均匀度差的产品纤维的结合力也相对差些,有纤维絮聚的部分受胶版的作用力就大些,黏到油墨量也多,就更容易掉毛掉粉。
3、改善纸张的匀度
匀度不好的纸张,表面均匀性差。印刷时,纸张表面与着墨的印版或橡皮布表面接触不匀,定量稍大部分的印迹一经摩擦,纸面就会产生颗粒状剥落,即“粉化”。如果纸张过分疏松,吸墨性过强,当使用的油墨黏度较低、印刷压力较大时,还会导致油墨渗透到纸张背面。
在改善纸张的匀度方面,根据纸机不同的实际情况,而相应采取如下不同的措施。
①针对不同的浆种,调整打浆工艺
公司使用的造纸原料有蔗渣浆、桉木化机浆、长纤维针叶木浆,不同的浆种采用不同的打浆工艺。
对于纤维较短的蔗渣浆和桉木化机浆尽量帚化,避免切断,尽量保留纤维的长度;
对于长纤维针叶木浆则要充分的帚化,且要适当的切断,有利于纤维的交织,提高纤维间的结合力。
②控制好上网浓度
纤维在上网时,浓度越大,絮聚的时间就越短,分散性就越差。在生产中,根据机型和产品定量的不同,要求控制不同的上网浓度。如抄50g/㎡的纸为0.45%~0.5%;抄55g/㎡的纸为0.5%~0.55%;抄60g/㎡的纸为0.55%~0.6%,一般都不能超过抄造定量的万分之一。
③各种浆料混合稳定
对在生产中使用的蔗渣浆、桉木化机浆、长纤维针叶木浆,根据产品的种类和定量的不同而规定好不同的配比,使用部分桉木化机浆能够增加纸张的松厚度和改善纸张的匀度,但由于化机浆含木素较多,用量过多时抄出来的纸发脆、强度低。为了使强度不至于降低,需要加入一定量的长纤维针叶木浆,长纤维对匀度又有影响,因此,必须确保各组分配比的稳定,避免因各种组分的不稳定而对产品的匀度、强度产生不良影响。
4、调整表面施胶工艺
在对表面施胶工艺调整前,表面施胶只加入氧化淀粉、表面施胶剂和增白剂,为了更好地发挥表面施胶的作用,又加入一定量的聚乙烯醇(PVA)、消泡剂、助留剂等,同时还选用一种带阳离子的表面施胶剂,它跟助剂配用有较好的流动性和成膜性,所以挂胶量有了很大的提高。淀粉的糊化浓度为10%左右,对淀粉的糊化温度和时间也作了相应的调整,最后把胶料稀释到9%左右再进行施胶。
根据产品的品种,经测定施胶量一般约为1.28~1.55g/㎡,比调整前的0.92~1.13g/㎡有比较大的提高,有效增强了成纸的印刷表面强度,调整表面施胶工艺前后对成纸印刷表面强度的影响对比如表2。
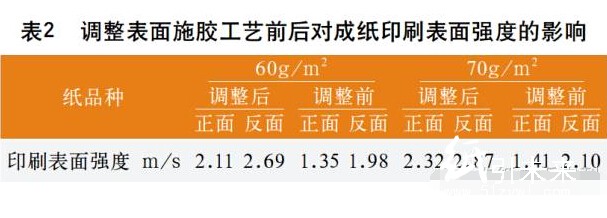
5、加入一定量的添加剂
在浆内加入一些添加剂,如增强剂、助留剂、阳离子淀粉等,有利于纸浆纤维的均匀交织,提高纤维的结合力,同时改善网部浆料的滤水性能,提高细小纤维和填料的留着率,使纸浆中的细小纤维和填料附着到较大纤维的表面上,减少纸页表面细小纤维和填料在网部的流失,从而提高纸张的表面强度。
6、加强产品生产过程的质量控制
①加强进厂原材料的检验
除常规项目的检测,浆的湿重也作为蔗渣浆的重要指标来检测,湿重过低时,纤维过短,影响成纸的强度。化机浆还要检测纤维束,纤维束坚硬,很难通过打浆完全帚化或筛选除去,成纸时容易留在纸面上,纸面上的纤维束在印刷时极易脱落造成糊版,因此化机浆的纤维束含量不能超过规定的0.05%。还要加强对填料细度的检验,填料通过325目筛要达98.5%以上,使用通过率过低的填料生产时,手掌在纸面上稍用力一擦,手掌就有一些白色粉末,有时还有一些填料小颗粒,印刷时就容易脱落黏到胶版上,造成糊版。
②加强产品灰分的检验
我公司根据不同的品种、不同的定量规定有相应的灰分范围,一般都在18%~24%。加入填料可以改善浆料的脱水,还有利于纸张的干燥,这样便可以提高车速,加入大量的填料,还可以大幅度降低生产成本。但填料加入过多则影响纤维与纤维的结合,加重了印刷时的掉毛掉粉。灰分超过27%时,切纸机的圆刀和长刀钝得很快,从切纸机处脱落的粉尘和纸屑会很严重,纸张吸附的粉尘和纸屑也会更多。因此,要求生产车间加强考核,要严格执行公司规定的产品灰分指标。
③提高产品的平滑度,减少两面差
为了提高产品的平滑度:
首先,各浆种要按一定的比例配比,加入化机浆的比例要适量;
其次,要保证各浆种的打浆度,要符合产品质量要求。特别是化机浆,由于纤维硬挺,对产品的平滑度影响较大,因此,要保证有足够的打浆度;
再就是要控制好纸页的水分,特别是进入压光机前的水分,并适当加大压光机的线压力;
还要控制好产品的干燥曲线,干燥过急、烘缸温度过高使纸页内部水分蒸发过快,纤维在蒸发的作用下,相互结合疏松,纸页表面起毛,影响纤维的取向,平滑度会下降;
另外,还可以通过选择成形网的织法、线径来减少细小纤维的流失,改善成纸表面的细腻程度。在某些机台,平滑度还可以通过提高产品的匀度以及张紧烘缸上的干毯来取得。
④适当提高压榨的线压力
纸机压榨的线压力不够,纸页脱水不良,影响纤维间的接触,减少了氢键的结合点,影响纸张的强度,也容易造成掉毛掉粉。因此,要求各机台尽量提高压榨的线压力,有效增加纸页的脱水量,降低纸页进入烘缸的水分,避免急干燥,还能有效增加纸张的紧度。
⑤保持压榨毛毯、干毯以及烘缸面的清洁
如果毛毯、干毯、烘缸面黏有脏物,会使已经结合良好的纸页表面受到破坏,影响纸页的表面强度。因此,要求毛毯保持清洁,各机台都安装有毛毯在线清洗系统,并定期使用毛毯清洗剂来清洗。对于烘缸刮刀要勤检查,保持刮刀与烘缸面贴合好,保持缸面的清洁,并及时清理刮刀上的粉尘和纸屑。