现在人力成本在一定程度要远大于材料成本,譬如拿着高薪的研发人员,很难衡量效率的管理人员等,所有的时间浪费都会转换为人员工资体现。
一个企业的员工薪酬可能要吃掉一大半企业利润,有的甚至全部,亏损企业就是。
说时间,不是让大家增加工作时间,最近大家996听得多了,对工作时长天然极具敏感。
这里说的不是一周40小时工作制,改为45小时工作制,而是说将原来做任何一件事情的时间减半。
譬如,产品生产周期由4天缩短为2天,或将某一机床的换模时间由30分钟缩短为15分钟,或将某一条产品流水线生产节拍由180秒缩短为90秒,或者将某一种例会会议时长由2小时缩短为1小时,或将某一任务流程流转时间由1天缩短为半天,等等,……时间就是金钱,时间就是竞争力。
时间降本的威力远胜于材料降本。
1/4开发时间减半
一个新产品研制周期决定了其研发成本和上市周期,前者代表了研发人员人力成本,后者决定了是否能够战胜同行,在市场竞争大潮中能否占得先机,体现出的价值无限。
这里面是有套路的,有的企业前面新产品上马快,属于拍脑袋决策,研发人员也是闭门干活,快是快了,新产品研制完成之时,就是正式开始了新产品的苦难历程。
缝缝补补三年,修修改改又三年,没有三、五年不会消停,有的甚至直接寿终正寝。
华为1997年以前,销售额虽然连年增长,但是产品的毛利率却逐年下降,人均效益只有思科、IBM、爱立信的六分之一到三分之一。
由于产品设计问题,华为曾经耗费5亿元对全网100万块程控交换机板卡进行整改;光传输和VPN系统因研发疏忽,客户大面积退货造成十几亿元的损失,大量服务人员在外,利润都交给了航空公司和酒店。
华为1998年邀请IBM帮助其实施IPD以后,产品研发周期缩短40%,研发费用下降50%,新品可以以最快的时间占领市场。
从此,华为研发发生了脱胎换骨的变化。你看,研发环节蕴藏了多少时间宝藏呀。
2/4生产时间减半
实体制造企业最大的时间消耗应该在车间一线,人多,产品线多,批量生产每天会有固定的制造时间。
如果一线300人,每天8小时工作制,一天就是2400人时,若能减少10%,也就是生产效率提升10%,那将会节约30个人出来,这将是一笔多大财富呀。
笔者由于工作关系,不管是自己工作过的单位,还是考察过的一些友商,通过实施精益生产,效率普遍提升30~50%不等,甚至100%都没有问题。
不是说原来干活有多慢,而是停工待料、模具换模、设备故障等等待造成的等待浪费时间太多,有效作业时间太少。
有的企业亏损,有的企业经营困难,孰不知自己手中有一个金矿却视而不见。精简生产制造时间,精益生产是一件利器。
福特1913年按照生产流水线设置的高地公园工厂投产后,将原先使用旧方法组装1台T型车至少需要12小时压缩到93分钟,实现每40秒下线一辆汽车,生产效率提高到775%。
丰田1945年,冲压换模时间3小时,1962年冲压换模时间缩短为15分钟,1971年换模时间又从15分钟变为变为3分钟,从而使多品种小批量生产成为可能。
三菱重工,用1年的时间将8轴镗孔机床的换模时间由24小时缩短到160秒。
有的企业改变生产布局,将包干制生产模式改为节拍化流水线生产,6个月内,生产效率提升200%,交付周期缩短50%,生产场地减少50%......,这样的效果你想要吗?
表1不同国家单台汽车装配工时比较
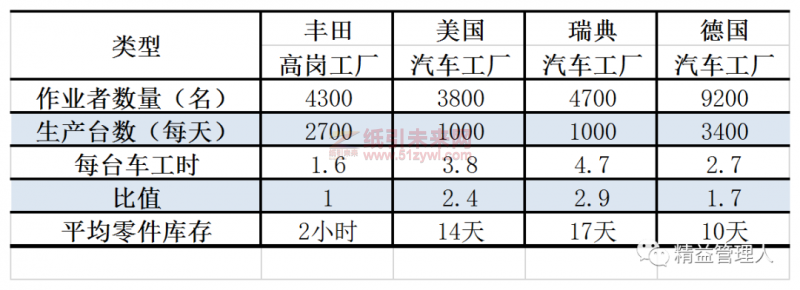
3/4库存滞留时间减半
有人说生产管理就是库存管理,它反映出一个企业运营管理的智商水平,可见库存管理之重要。
库存是供应链链条上的黏合剂,库存左手边是履约交付,反映出支撑营销攻城拔寨的能力。
库存多,代表及时履约能力强,销售喜欢,但财务不喜欢,可能赚的可怜的一点钱全砸在库存上了;右手边是生产库存管理,反映出供应链库存周转的能力。
库存少,代表库存积压资金少,库存周转快,但及时履约能力风险加大,财务喜欢,但销售不喜欢,红海市场能拼的就只剩下“交付快”这一利器了。
库存问题永远在销和产之间寻求平衡,不是非黑即白,也不是非白即黑,而是一个灰度控制问题。
库存滞留时间控制方向:
计划层面上:对于营销部门,制定客户需求预测计划准确率的指标,制定成品库存滞留时长指标;监督项目计划部门计划调整及时性和物资采购部门、仓储部门无效物料入库数据。
工作方式层面上:
对于物资采购部门,制定采购规则,明确安全库存数量,制定定期不定量、定量不定期对物料的使用原则等,定期、不定期抽查执行结果;
对于仓储部门,根据月度盘点结果,制定未按先进先出考核原则;
对于研发、技术部门,升级换代遗留下来的物料与之部分绩效挂钩;对于车间制造部门,制定每年成品制造周期缩短指标;
对于生产部门,考核其公司整体库存控制指标,意在促进其不停曝光使库存增加的各项隐患来源,同时定期做好呆滞物料代用、置换、变卖、报废等工作。
计划做得好,供应链反应快,交期缩短了,库存周转率也上去了,不仅履约完成得好,运营成本也大幅下降。
一个12亿年销售额的生产制造企业,库存周转率若从每年6次提升12次,75%材料成本,支撑企业运营的流动资金从(12亿元/6次)*75%=1.5亿元,下降到0.75亿元。
7500万的现金能干多少事,投资新业务或及时支付供应商货款等等,要知道现金流断裂时,很多企业死在1分钱身上。
日本松下采用SCM供应链管理系统以后,一线经销商信息反馈到总部从1个月降为1天,以及通过对生产周期的压缩,2003年共为松下节省了1201亿日元的库存成本,而其当年利润总额才只有1955亿日元。
4/4流程时间减半
企业中的信息流转,看不见,摸不着,其实这里面可能是一个巨大的时间消耗器。
企业经营者对眼睛可见的工作时间要求较高,并且要求一再压缩。企业领导常挂在嘴边:研发周期要加快,设计周期能否再缩短几天,车间制造时间能否节拍再快一点,发货时间……,等等。
可是你知道,还有很多时间黑洞你根本没有在意吗?
譬如,营销不去客户那儿提前求证项目交付具体时间,一切都不是空穴来风,往往客户一催就是急单,营销对前端信息没有主动跟盯意识,白白让有用的信息时间流逝,有的营销人员收到客户的需求信息,往抽屉一放,忘记往下游传递了,这个时间浪费可就不是1小时、3小时了,有的以周、月统计,等反应过来,没办法,再压后端的刚性时间,产品质量能有的好?
研发部门,不愿意公开自己的研发计划,好像这是自己的一块私留地,等产品研制出来以后,物料采购不方便、生产制造不方便,材料应用和工艺设计还有诸多明显的提升空间,这就是信息保密的结果,后面全部用金钱来买单。
有的流程需要经过20几个人审批,时间长达一个多月,不仅费时还误事。
某航空零部件企业,精简订单交付流程,将94个流程步骤缩短为28个,与供应商的信息传递从4-6天缩短为几分钟;客户询价到报价时间由48个小时缩短为6个小时,生产时间缩短50%,订单交付准时率从15%提升到85%。
一些企业职能审批信息流从来没有像车间制造节拍一样,以分钟计、以秒计,基本上是按天甚至周计。
如果用价值流程图展示出来,一定会让你惊愕到掉下巴!
说实在的,信息传递时间的浪费是所有浪费中最大的。不经意间、习惯的的东西才是最可怕的。
贸易战、加关税、市场寒冬、客户强势、新冠疫情等,外界我们无法改变,能够改变的只有我们自己。
也许我们认为一切我们做的已经够好,没有什么可以改进的地方了。
大野耐一认为的确有些错觉是潜藏在常识之中的,于是才能够让人们将它当成理所当然的规律去照做。
经营企业,要有不求天、不求地、不求人,只求己的心态。
在市场竞争日趋激烈的今天,一味依靠提升销售量增加利润的方式难度很大,往往不是自己说了算,更应该做的事竭尽全力降低时间成本,这个自己可以做主。
时间浪费最隐蔽、最费钱、最无底洞。
如果你不能迅速把产品开发时间减少50%,交货周期减少50%,生产时间减少50%,库存周转率提高1倍,那么你一定是哪儿做错了。